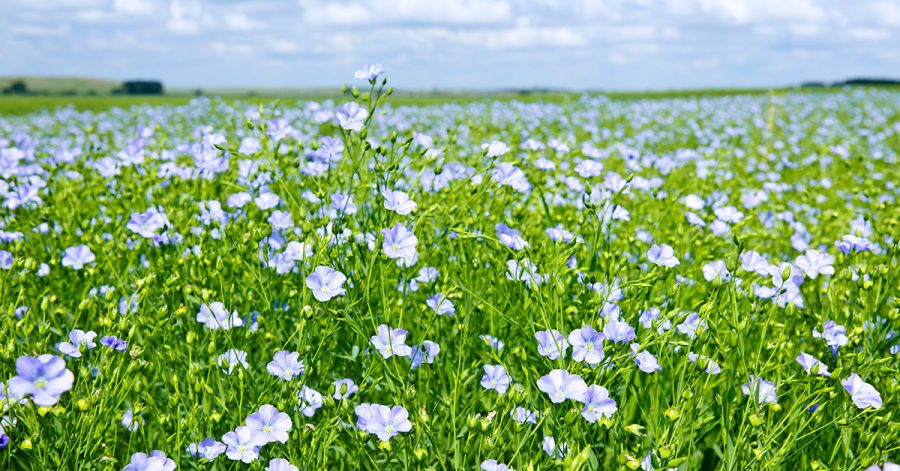
The Egyptian flax plant grows to a height of up to 1.2 m. Its leaves are long and thin, green in colour, while the flowers are light blue; the seed is contained within the fruit, which has a round size of about 5-9 mm. The flax plant is cultivated for both seed and fibre. The term ‘flax’, commonly used in our industry, is used to identify both the plant and the unspun flax fibre. Flax fibre consists of a central core, an inner bark and an outer bark; for yarn production, the inner bark must be separated from the core and the outer bark. These different layers, however, are held together by a ‘glue’, formed by lignins and pectins, and to dissolve this bond, the stems must be macerated. Flax is sown in Europe around mid-March, and in Egypt in January. The seeds are scattered very thickly so as to encourage the natural upward growth of the plant, in order to obtain the longest possible fibres. One of the first processing steps is maceration (retting), which usually consists of prolonged exposure of the stem to moisture. This different treatment gives the Egyptian fibre a lighter appearance, while the European fibre is darker in colour. This process produces a coarse fibre composed of long, woody fibre called ‘shive’ and a short flax fibre called ‘scutching tow’ (rescutched tow or Arusse).
FROM SOWING TO SPINNING
Characteristics and properties of flax
Flax processing stages: from sowing to spinning
The main fibres used are distinguished by their origin, which can be Egyptian or European.
In Egyptian fibre, the flax plant is literally uprooted (not cut), to obtain the maximum fibre length, and is macerated immersed in water.
Water is the most common practice for steeping and produces fibre of the highest quality. It is preferable to do this in stagnant or slowly moving water, such as ponds, swamps and streams. As a rule, the more stagnant the water source, the more abundant the bacterial fauna and the faster the maceration process, which generally lasts from a few days to a couple of weeks, depending on the water temperature.
European fibre, on the other hand, is macerated on the ground, only thanks to the dew that settles on the stems during the night.
This method is preferred in areas where water sources are limited, but which enjoy warm temperatures during the day and abundant dew at night.
The flax stems are spread evenly over a field, where the combination of air, sun and dew causes fermentation, which dissolves much of the stem, within 2-3 weeks.
After the retting process, the stems are air or mechanically dried and are usually stored for a period of a few weeks to months to allow polymerisation.
After polymerisation, the woody stems that still cling to the flax fibres are further broken in the scutching process by passing them through rollers that crush the woody part into smaller pieces (shives), so that they can be removed more easily.
Scutching tow is also used for the production of ropes and twines, but being coarser, it is used in products where a high degree of homogeneity is not required, such as ropes and twines of large gauge.
Long fibres go through a process called combing (heckled), which uses combs to separate the short fibre (comb tow or machine tow) from the long fibre (long fibre).
Both long and short fibres are straightened in several passes, becoming uniform and homogeneous, before being spun.
We at Lottini srl have always followed all stages of flax processing, right from sowing.
In this month of the year, the new crop of Egyptian fibre is ready for cutting, more precisely for ‘pulling’. The plant is not cut, but weeded, to get the maximum length of fibre, hence the term ‘pulling’ from the English ‘pull’.
This happens about 100 days after sowing and thirty days after flowering.
Within forty days after pulling, it will be ready for processing.